By: PR Fueled
Heavy-duty conveyor rollers are critical components in the material handling industry. These conveyor rollers are designed to support and guide the conveyor belt, ensuring efficient and smooth transportation of heavy and bulky materials. Used extensively in various sectors, including mining, manufacturing, and logistics, heavy-duty conveyor rollers enhance operational efficiency by reducing downtime and maintenance costs. They are built to withstand harsh environments and high load capacities, making them indispensable in industrial applications.Â
Design and Construction of Heavy Duty Conveyor Rollers
Material Specifications:
Heavy-duty conveyor rollers are primarily constructed from materials like steel, aluminum, and nylon, each chosen for its unique properties:
Steel: Steel rollers are known for their incredible strength and resistance to wear and tear.Â
Nylon: Nylon rollers are used in environments requiring quieter operations and resistance to chemicals.Â
Load-Bearing Capacities:
The load-bearing capacity of heavy-duty conveyor rollers is a critical design element. These rollers are engineered to support substantial weights:
Standard Load Capacities: Depending on the specific application, rollers can handle loads from a few hundred kilograms up to several tons.Â
High Load Applications: For extremely heavy loads, reinforced steel rollers with thicker walls and larger diameters are used.
Applications of Heavy Duty Conveyor Rollers
Mining:
Underground Mining: Conveyor rollers facilitate the movement of extracted materials from the mining site to the surface for further processing.
Surface Mining: They are used in conveying systems that transport materials from open-pit mines to processing plants or storage areas.
Processing Plants: Heavy-duty rollers are employed in processing facilities to move raw materials through various stages of crushing, grinding, and sorting.
Construction:
Building Sites: Rollers are used in conveyors that transport materials across large construction sites, reducing the need for manual handling and increasing efficiency.
Concrete Production: They facilitate the movement of raw materials into mixers and conveyors that deliver concrete to various parts of the construction site.
Demolition: Heavy-duty rollers are used in conveyors that transport debris and waste materials away from demolition sites for recycling or disposal.
Manufacturing:
Assembly Lines: Rollers are used in conveyor systems that move products between various assembly stations, supporting efficient and continuous production processes.
Material Handling: Heavy-duty rollers help in transporting raw materials, components, and finished goods within manufacturing facilities.
Packaging: They are used in conveyor systems that move products through packaging lines, ensuring that items are efficiently packed and prepared for shipment.
Conveyor Impact Rollers in Heavy Duty Applications
Design and Functionality:
Conveyor impact rollers are specifically engineered to withstand the high impact forces that occur when heavy materials are loaded onto the conveyor belt. Their design includes:
Shock Absorption: These rollers are equipped with a resilient outer layer, often made from materials like rubber or polyurethane, which absorbs the impact energy. Reinforced Construction: The core of the impact roller is typically made from high-strength steel or other durable materials, providing the necessary structural integrity to handle heavy loads.
Multi-layer Design: Some impact rollers feature multiple layers of cushioning materials, enhancing their ability to absorb shock and extend the lifespan of both the roller and the conveyor belt.
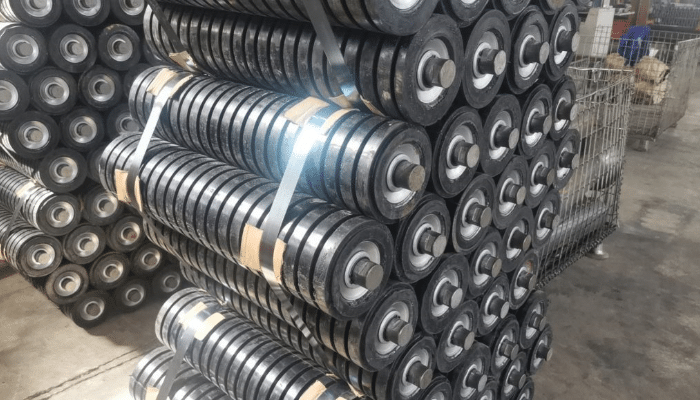
Key Features for Heavy-Duty Use:
Impact rollers used in heavy-duty applications possess several key features that make them suitable for demanding environments:
Durability: These rollers are built to last, with robust construction that can withstand the rigors of continuous heavy-duty use.Â
Enhanced Sealing: High-quality seals are used to protect the internal bearings from dust, dirt, and other contaminants.Â
High Load Capacity: Impact rollers are designed to support significant weights, making them suitable for applications where large and heavy materials are regularly transported.
Manufacturers of Heavy Duty Conveyor Rollers
Several leading companies are recognized for their expertise in producing heavy-duty conveyor rollers:
GRAM Conveyor:Known for their high-quality conveyor systems,offers a wide range of heavy-duty conveyor rollers designed to handle demanding applications with high reliability and efficiency.
Rexnord Corporation: Known for its durable and reliable conveyor components, Rexnord offers a wide range of heavy-duty rollers designed for high load capacities and harsh environments.
Flexco: Specializing in conveyor belt solutions, Flexco provides heavy-duty rollers that are built to last and enhance the efficiency of material handling systems.
Continental Conveyor: This company offers a variety of conveyor rollers, including heavy-duty models that are designed for mining, construction, and industrial applications.
PROK: With a focus on quality and performance, PROK manufactures heavy-duty conveyor rollers that are used in some of the demanding industries worldwide.
Price Considerations for Nylon Conveyor Rollers
When selecting conveyor rollers for heavy-duty applications, understanding the price considerations for nylon conveyor rollers is crucial. This involves examining various cost factors, comparing nylon with other materials, and budgeting for an efficient and cost-effective conveyor system.
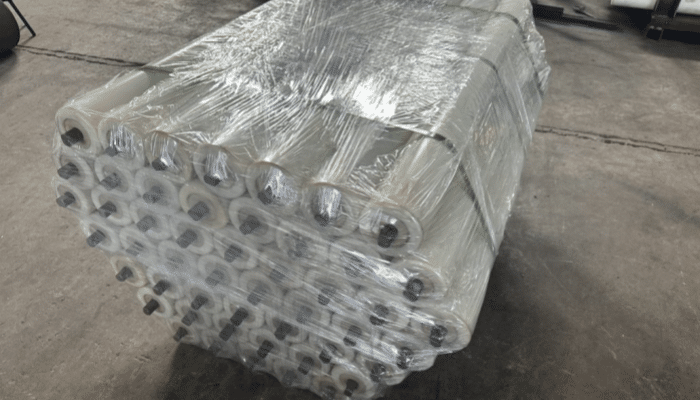
Cost Factors for Nylon Conveyor Rollers:
Material Quality: High-grade nylon used in the rollers is more expensive due to its superior properties, such as high wear resistance, chemical resistance, and reduced noise levels during operation.
Load Capacity: Nylon rollers designed for higher load capacities require additional reinforcements and advanced engineering, contributing to higher costs. Heavy-duty applications often necessitate rollers with enhanced structural integrity, which can be more expensive.
Customizations: Specific customizations like special sizes, additional coatings for enhanced durability, or unique designs to meet particular industrial needs can increase the price. Custom engineering and fabrication add to the overall cost.
Production Techniques: The manufacturing process, including the precision of the molding or machining process, impacts the price.
Comparison with Other Materials:
Comparing nylon rollers with those made from other materials provides a clearer understanding of their cost-effectiveness:
Steel: Steel rollers are generally more expensive than nylon rollers due to the cost of raw materials and the complex manufacturing processes involved.Â
Polyurethane: Polyurethane rollers are often more expensive than nylon due to their exceptional shock absorption and wear resistance.
Published by: Nelly Chavez