Maintaining a sanitary process environment is paramount for any food, dairy, or beverage processor. Ensuring product quality, purity, and safety requires a precise and reliable cleaning approach, and this is where Clean-in-Place (CIP) systems prove invaluable. These automated systems streamline the cleaning of essential processing equipment, eliminating bacteria and contaminants without disassembly. For Central States Industrial (CSI), providing effective CIP systems means supporting processors with optimized cleaning solutions that keep operations safe, productive, and efficient.
Understanding the Importance of CIP Systems
A Clean-in-Place (CIP) system is designed to clean the sanitary lines, vessels, and equipment typically found in processing plants without dismantling piping or other components. CIP systems use a series of cleaning, rinsing, and sanitizing cycles to thoroughly clean internal surfaces by circulating solutions through the same piping path as the product. This reduces manual cleaning requirements and ensures consistent sanitation, minimizing contamination risk and upholding product integrity.
CIP systems operate in process piping, tanks, heat exchangers, and more, preventing potential contaminants from lingering on surfaces and reducing the likelihood of spoilage or recall events. In addition to reinforcing food safety standards, these systems facilitate smoother, more efficient production by reducing manual intervention and the potential for human error.
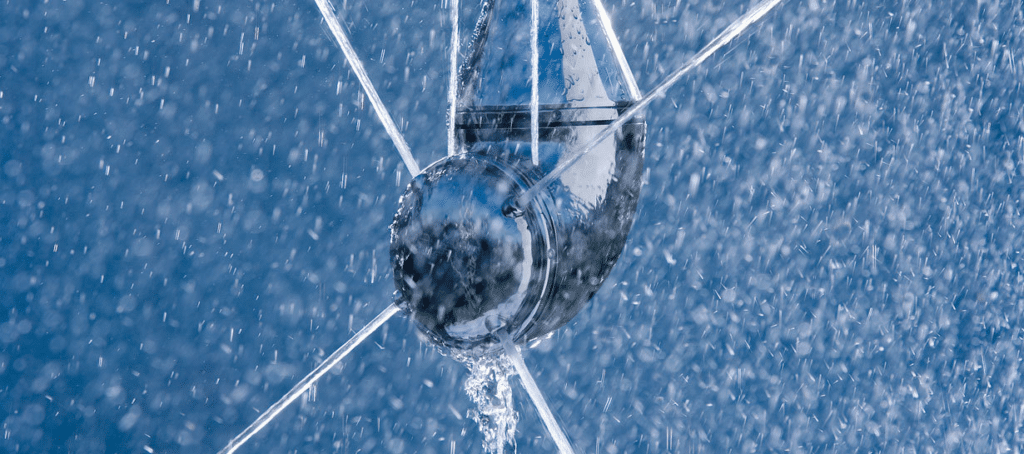
Advantages of Implementing a CIP System
In the food, dairy, and beverage industries, CIP systems provide several crucial advantages:
- Reduced Risk of Human Error
Automating the cleaning process significantly reduces the chance of errors that can compromise product safety. By replacing manual steps with automated controls, CIP systems deliver consistency in cleaning, lowering the risk of contamination and the need for rework. - Enhanced Employee Safety
Cleaning chemical exposure poses risks to workers in manual cleaning scenarios. CIP systems mitigate this by confining the cleaning solutions within the equipment and piping system, keeping employees safer and reducing the likelihood of handling-related accidents. - Increased Production Time
With automated cleaning cycles, less production time is lost to downtime for manual cleaning. This advantage enables processors to focus on production output, achieve higher efficiency, and ultimately make more of their product available in less time. - Reliable Product Quality
CIP systems contribute to dependable product quality by establishing a repeatable and verifiable cleaning process. Consistent cleanliness reduces the chances of contamination, leading to fewer recalls and supporting consumer trust in the brand. - Utility Savings
Another key advantage of CIP systems is resource conservation. Since water and energy use are minimized through cycle control, CIP systems help processors achieve cleaner equipment with lower resource expenditure, promoting sustainability without compromising on cleanliness standards.
CSI provides insight through a five-step CIP process for a more comprehensive overview of the CIP system’s functionality and process. This guide covers the essential steps in a CIP cycle and how each phase contributes to achieving an immaculate processing environment.
The Central States Industrial Story
Central States Industrial began with a modest vision in Jim and Shirley Cook’s garage. From its 500-square-foot origins, the company has grown into an industry leader, headquartered in an 80,000-square-foot facility with five additional locations across the United States. CSI’s commitment to advancing hygienic process solutions has made it a trusted partner to thousands of customers worldwide. Their dedication to innovation and quality, honed over decades, is embedded in every solution they offer, including CIP systems supporting some of the largest global food, dairy, and beverage manufacturers.
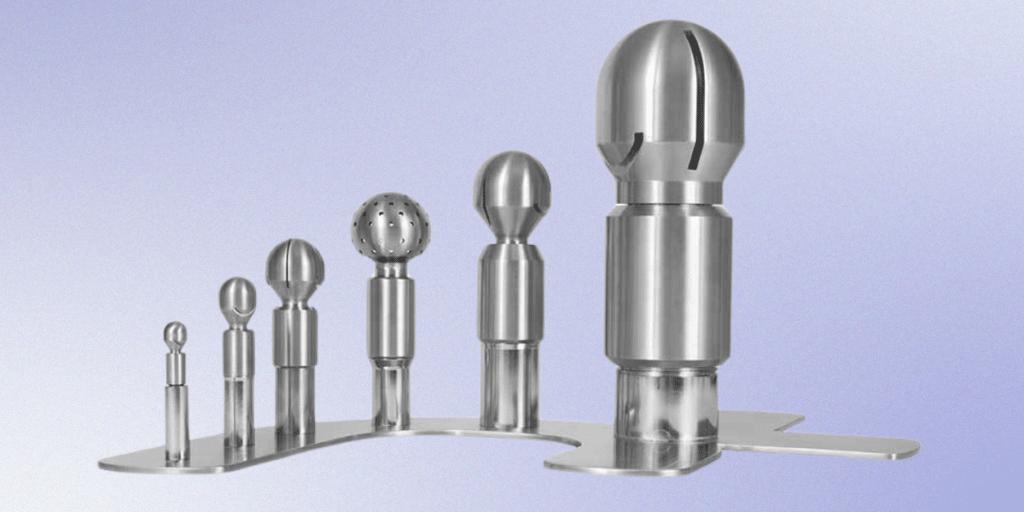
Why Choose a CIP System from CSI?
A commitment to quality, consistency, and customer safety is at the heart of CSI’s CIP offerings. With CSI’s CIP systems, food, dairy, and beverage processors can streamline their cleaning protocols, ensuring sanitation without the complexities of manual intervention. By prioritizing utility savings, product safety, and minimal downtime, CSI enables processors to keep their production environments clean and efficient.
A well-designed CIP system is indispensable for those aiming to uphold stringent hygiene standards while optimizing resources. CSI’s expertise in this field gives processors the peace of mind that each cleaning cycle protects product quality, employee safety, and operational efficiency.
Choosing a CIP system from CSI means partnering with an industry expert who understands the rigorous standards of sanitary processing and the impact of reliable cleaning solutions. With an unwavering focus on sustainable, efficient practices, CSI provides solutions that help processors keep pace with production demands while safeguarding product integrity.
A Trusted Partner in Sanitation Solutions
Central States Industrial’s journey from a small garage operation to a leader in sanitary processing equipment speaks to the values of quality, dedication, and customer trust. Their CIP systems reflect this legacy, allowing food, dairy, and beverage processors to meet the highest standards in sanitation. With a focus on minimizing risks, enhancing safety, and reducing resource use, CSI remains committed to helping processors maintain a cleaner, safer, and more productive environment.
Through solutions like the 5 step CIP process, Central States Industrial continues to support its partners in achieving reliable, repeatable cleanliness while fostering a legacy of excellence in the industry.
Published By: Aize Perez